Stainless steel electrolytic polishing is mainly to be polished workpiece as the anode, insoluble metal as the cathode, the two poles are immersed in the electrolytic polishing tank at the same time, through direct current, resulting in selective anode dissolution, anode surface brightness increases, this process is the opposite of the plating process.
Electrolytic polishing is to put the workpiece to be polished into a special conductive solution (electrolyte > In, the workpiece is connected to the positive electrode of the power supply (anode > The negative electrode (cathode) of the power supply is connected to an insoluble conductive material, and through the current, the surface of the workpiece can be dissolved under certain conditions and the surface is smooth.
The significant advantage of the electrolytic polishing process is that when the power supply has sufficient power, the duration of the process is independent of the size of the surface to be machined, and a large number of small workpieces or several large workpieces can be loaded at the same time in the tank containing the electrolyte. In many cases, the productivity of electrolytic polishing is much greater than that of mechanical polishing. The shape of the machined surface has little effect on productivity.
In electrolytic polishing, the ability of polishing to smooth the surface is ideally insoluble at the bottom of the depression, and the protruding part is dissolved, so as to achieve microscopic leveling.
Operation method:
The lead plate is the cathode (negative electrode), the workpiece is the anode (positive electrode), 60-65 degrees, the current density is 10-25 amps/square decimeter, the voltage is 8-10 volts, and the time is 5-8 minutes.
Process flow:
(Oil removal and rust activation → washing → drying) → electrolytic polishing → washing → passivation → washing → neutralization → washing.
Operation precautions:
1. The stainless steel workpiece should be removed from the surface of the workpiece as far as possible before entering the polishing groove, because the workpiece carries too much water may cause serious pitting on the polishing surface, and local etching leads to the scrap of the workpiece.
2. In the electrolytic polishing process, the stainless steel workpiece as the anode, the iron and chromium elements contained in it are continuously transformed into metal ions dissolved in the polishing liquid and not deposited on the cathode surface. With the polishing process, the concentration of metal ions continues to increase, and when it reaches a certain value, these metal ions continue to precipitate from the polishing liquid in the form of phosphate and sulfate, settling at the bottom of the polishing tank. For this purpose, the polishing liquid must be filtered regularly to remove these solid sediments.
3. During the operation of the polishing tank, in addition to the continuous consumption of phosphoric acid and sulfuric acid, the water is lost due to evaporation and electrolysis. In addition, the high-viscosity polishing liquid is continuously lost by the workpiece, and the polishing liquid level continues to drop, so fresh polishing liquid and water need to be added to the polishing tank frequently.
Electrolytic polishing process uses a high current density to maintain the dynamic balance between the formation and dissolution of the workpiece surface film, so that the workpiece surface retains a layer of a certain thickness, dense film. Therefore, the surface conditions of the workpiece must be good and consistent everywhere, the surface temperature of the workpiece in contact with the electrolyte must be uniform, and the small and dense bubble layer on the electrode surface must be removed as far as possible when the current density is high. In order to achieve this purpose, a high relative motion between the electrolyte and the workpiece surface should be maintained; The electrolytic polishing groove should have a considerable depth to ensure that there is enough groove liquid and enough space when the electrode is vibrating; The cleaning tank should be as close as possible to the I electrode vibration equipment installed at both ends of the tank body, vibration anode (workpiece) when electrolysis, sometimes also known as moving anode or shaking anode; The acid tank is heated with steam or hot water through a lead pipe. Electrolytic polishing needs to be heated at the beginning, and needs to be cooled after reaching the rated temperature.
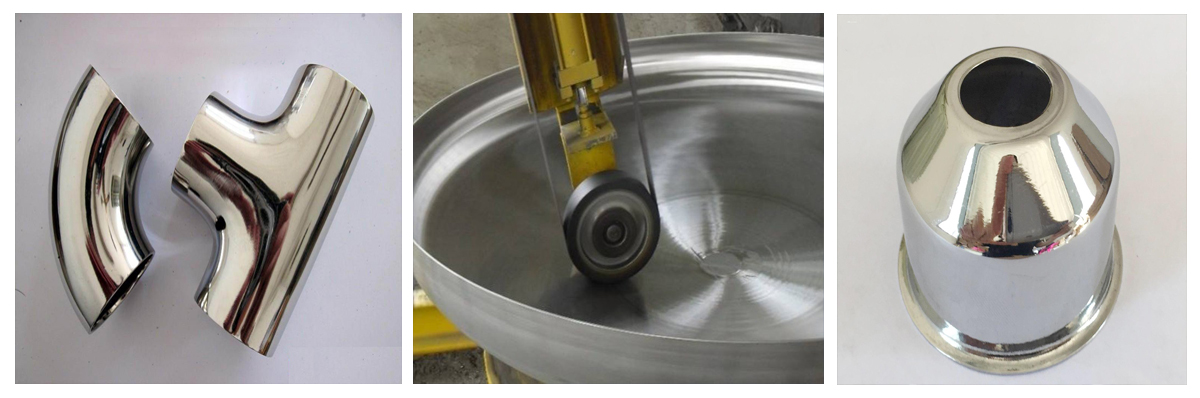
Electrochemical polishing compared with manual mechanical polishing, can play the following advantages,
1. The product has the same color inside and outside. Please clean light Xian, light 洚 lasting, clear appearance;
2. The burrs in the threads dissolve and fall off in the electrolytic polishing process, and the threads are loosened to prevent the phenomenon of biting between the threads.
3. Enhanced corrosion resistance of polishing surface
4. Compared with mechanical polishing, high production efficiency and low production cost.
Maintenance of stainless steel electrolytic polishing liquid:
(1) Stainless steel workpiece must be thoroughly degreased before electrolysis polishing. And clean with detergent, so as not to stain the polishing tank.
(2) The relative density of the electrochemical polishing fluid is often measured during use. If the relative density is less than the specified value. It shows that the electrochemical polishing liquid contains too much water, and the solution can be heated to more than 80° by evaporation. The excess water is removed, and the insufficient volume can be supplemented with phosphoric acid and sulfuric acid in accordance with the ratio of the instructions, before the workpiece enters the electrochemical polishing tank. It is recommended to drain or blow dry the moisture attached to the workpiece first. If the relative density is too high, exceeding the value specified in the manual, it means that the water is too little, a small amount of water should be added appropriately, so that the relative density can be reduced to the limited value, and conditional tests should be conducted according to the periodic analysis of the solution, and timely adjustments should be made according to the results.
(3) The aging of the solution, due to the dissolution of the stainless steel surface during the polishing process, the content of iron, nickel and chromium in the solution will gradually increase, and the solution will gradually lose its polishing ability. No matter how to increase the current voltage and increase the temperature, it will not help to restore the polishing ability. Analytical solutions, such as iron content of more than 60g/L, trivalent chromium content of more than 25g/L, indicating that the solution has been aged, in the presence of high concentrations of phosphoric acid. Iron and chariot (trivalent) exist in the form of acid ferric dihydrogen phosphate Fe(H2PO4)3 or chromium dihydrogen phosphate Cr(H2PO4)3, and are not easy to precipitate. Only when iron phosphate or chromium phosphate is formed will it precipitate at the bottom of the tank, and the electrolytic polishing liquid with low phosphate concentration has self-purification ability. For polishing fluid regeneration, restore polishing ability, there are two methods to choose from. One method is to dilute the solution with appropriate water, reduce the acidity, iron, chromium, nickel and other impurities can be locally phosphate precipitation, remove the bottom of the tank precipitation, and then heat evaporation water, restore the original relative density, this method is more complicated and cumbersome operation, need to consume large energy and time. Another method is to replace part of the solution, it is best to retain 20% of the old electrolytic polishing liquid, and add 80% of the new solution. It can be processed with little or no power, and normal polishing can be achieved quickly.
(4) Clear the cathode lead plate, in the polishing process of the cathode lead plate will deposit a thick layer of iron, nickel, chromium, phosphate and other impurities, affecting the cathode surface conduction, resulting in a drop in current, so that the polishing surface of the anode current density is also not up, strict electricity affects the polishing quality, so • play in time to remove the sediment on the cathode plate, sometimes formed a hard thick film, to strong knock to remove. Finally rinse it off to keep the entire circuit smooth.
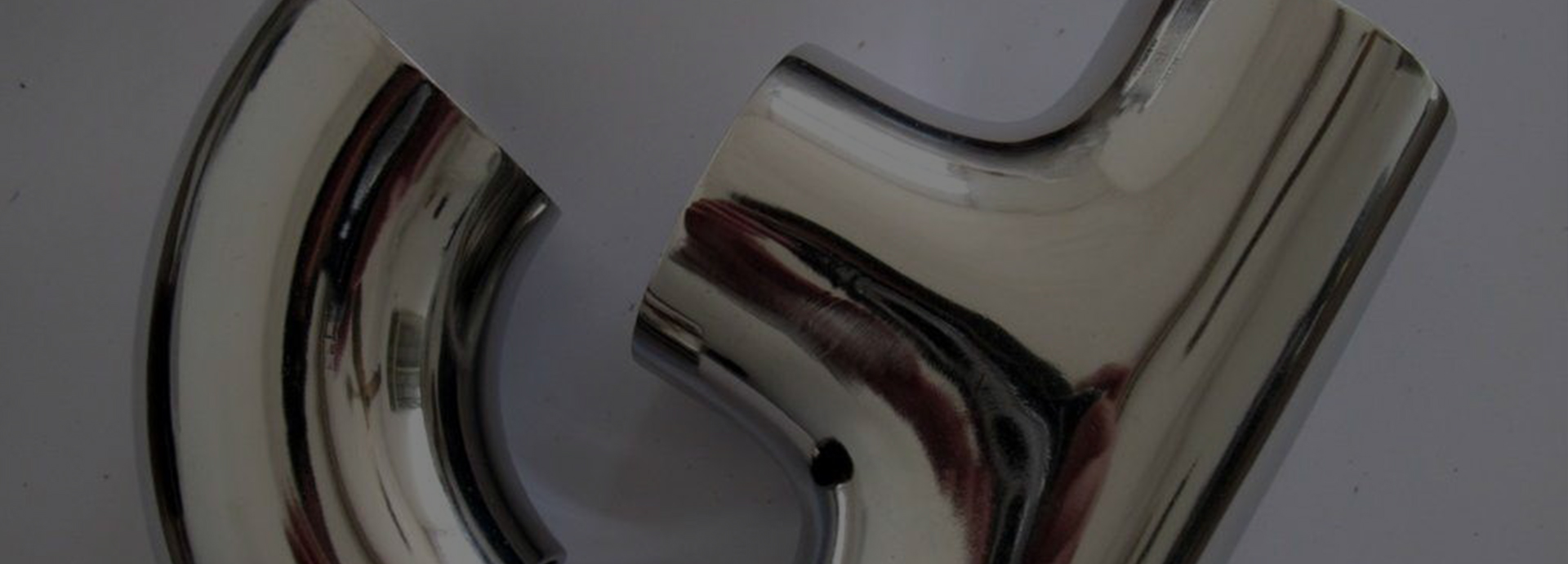
(5) The ratio of cathode to anode. The cathode area is controlled in 1/2 to 1/3.5 of the anode area, in this case. The growth of trivalent chromium can be prevented, and too much trivalent chromium is oxidized to hexavalent chromium on the anode surface. Too much trivalent chromium. Easy to make the polishing liquid aging.
(6) The distance between the anode and the cathode. The distance between cathode and anode is too large, the resistance increases, and the power consumption increases. The solution is easy to heat up, affect the polishing quality, the distance is too small, easy to cause short circuit ignition, burn black products. The distance between the cathode and the anode is 100 ~ 300mm.
(7) pictographic cathode, for polishing some complex large workpieces, pictographic cathode can be made to maintain a uniform distribution of anode current. In particular, the inner cavity workpiece has an appropriate pictographic cathode arranged in the inner cavity. So that all parts of the cavity polishing consistent.
(8) The power supply should be cut off from the outlet slot. In electrochemical polishing, due to the high current density, the feeding current is larger. Therefore, when the workpiece is in and out of the polishing tank, the power supply should be cut off first, and the fixture should not be hung or picked with electricity to prevent the generation of electrical sparks, resulting in electrolysis, and the hydrogen and oxygen mixture gathered on the surface of the tank will explode.
(9) Control the bath temperature. Due to the strong current passing through the tank, the tank will heat up, and cooling measures should be taken in continuous operation, using a refrigerator to cool the heating tank. The temperature of the polishing liquid should be properly maintained within the limited process range. The polishing and leveling rate of the stainless steel surface is maintained normally, so as to effectively reduce the temperature of the electrolyte, reduce the thickness of the anode mucosa, accelerate the diffusion of the anode dissolved products, accelerate the solution convection, and facilitate the retention of bubbles on the thousand (E) pole. Avoid spots' hemp I temperature is too high, will lead to overheating of the solution, accelerate the transformation of M chromium to 3 chromium, easy to produce surface corrosion. Too low temperature increases the viscosity of the solution. The thickening of the anodic surface mucosa is not conducive to the diffusion of the anodic solution, and the leveling effect is significantly reduced.
(10) Control the appropriate anode current density. In electrochemical polishing of stainless steel parts, the anode current density is almost proportional to the dissolution of the metal. Only the anode current density is selected and controlled in a certain anode potential zone. In order to obtain good electrochemical polishing quality, the optimal value of anode current density depends on different electrolyte formulations. Through the actual polishing, the best value is determined by observing the polishing. The anode current density is too small, the surface of the part has a general anodic dissolution, and the polishing effect is not achieved. The anode current density is too large, the mucosa is broken down, oxygen is precipitated violently, the surface is overheated, resulting in the diffusion of electrolytic polishing liquid, the mucosa is destroyed and no longer exists, electrochemical corrosion occurs, resulting in black, gray...
(11) Anode movement. The anode movement accelerates the diffusion of the anode dissolved products, plays a stirring role, effectively eliminates the residual bubbles on the anode surface, avoids the generation of air flow streaks, and prevents local overheating caused by surface overdecay. Anode movement helps to improve the anode current density and the electrochemical polishing surface quality of high stainless steel parts.
(12) The harm of chloride ions. Chlorine ions are not allowed to exist in the electrolytic polishing liquid of stainless steel, which can destroy the protective mucosa formed on the surface of the electrochemical polishing, so that the surface of the stainless steel forms the pitting of the corroded parts. Chlorine ions can be removed by oxidation to chlorine gas at high current density of the anode. The source of chloride ions may be the human tank after washing with hydrochloric acid, or the introduction of impurity chloride ions in the raw material.
(13) If the newly prepared electropolishing liquid does not have a chemical reaction to produce trivalent chromium, it can not obtain a good polished surface. Only when there is a certain amount of trivalent chromium in the electrolysis solution, can the ideal polishing surface appear. This is why the newly equipped electrolytic polishing liquid must be fully electrolyzed before normal polishing work can be performed. Chromium trivalent is green. They give the solution a yellow-green color in the electrolyte. This is why electrolytic polishing can only be done after energized treatment. "The best polishing quality is in the middle stage of the electrolytic process. At this time, according to the chemical analysis data, the color of the electrolyte, if the color is mainly yellow, indicating that the electrolyte contains high C0+, can add gelatin or glycerin suitable for M+, so that part of the hexavalent chromium is reduced to trivalent chromium, or through the large cathode and small anode electrolysis to produce trivalent chromium. If the color is dark green, it indicates that the electrolyte contains high hexavalent chromium, and the trivalent chromium part can be converted into hexavalent chromium by Dayang minimal cathode electrolysis polishing liquid, and the polishing quality of the solution can be improved.
(14) Metal removal amount. When the anode current density is 20A/dmz and the time is 4min, observed with a tool metallographic microscope, the metal removal amount of the inner diameter of the threads of stainless steel parts is about 0.01 mm per minute, while the outer diameter of the threads is 0. 002mm, and the tooth shape is basically unchanged. Only the top of the tooth is slightly blunted • The anode current density increases, and the amount of metal removed increases proportionally ^ For the size of precision stainless steel parts, the amount of metal removed after electrochemical polishing should be considered
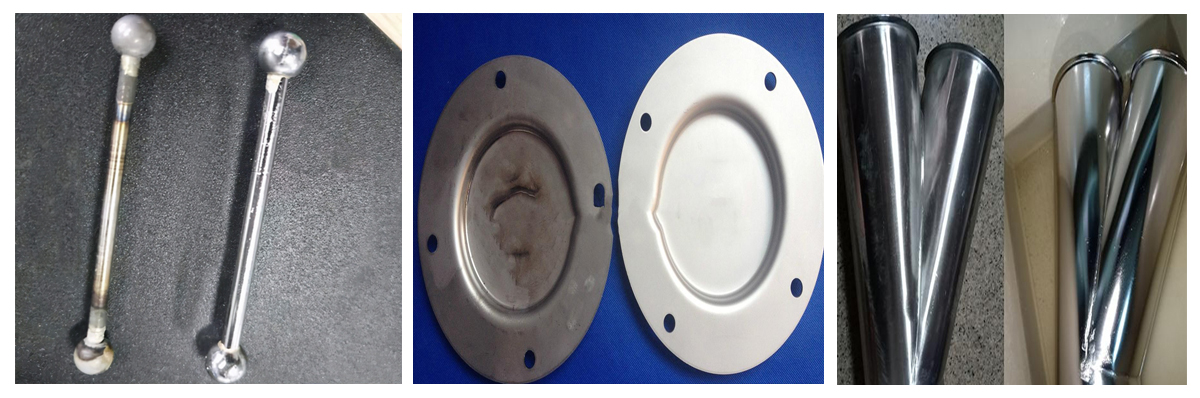
Power supplies, equipment and fixtures for electrochemical polishing
(1) Power. Polishing on the waveform of the power supply is not strict, so the general use of DC generators, silicon rectifier or thyristor rectifier can be. Power supply voltage No load requirement ○ 20V adjustable, the load with load is 8 ~ 10V working voltage. The operating voltage is lower than 6V, the polishing rate is slow, and the brightness is insufficient.
(2) electrochemical polishing groove. It can be welded from polyvinyl vinyl hard plate, which is equipped with three electrode rods, the middle is a movable anode rod, connected with the power anode, and the two sides are cathode rods, and connected with the power cathode. There should be a heating and cooling device on the tank. Titanium heating tube can be installed for heating, and titanium tube with cold water can be installed for cooling. Can also be made of 5mm thickness of steel plate inside and outside jacket groove, the inner groove is lined with 5mm thick lead, or lined with soft thickness of 3mm PVC plastic sheet, the jacket can be water and steam, in order to heat and cool, you can freely control the temperature of the polishing liquid in the groove.
(3) Fixture materials "Clamp made of mendelevium alloy or pure titanium material is more ideal" they conduct electricity well, have a certain elasticity and rigidity. Resistant to plum erosion. Long life. Aluminum or titanium ions into the electrolytic polishing liquid has no adverse effects. It is not appropriate to use copper, brass or phosphor copper as a fixture, copper ions into the electrolyte, precipitation on the cathode, in the power off parts of the moment, the stainless steel surface will immediately replace a layer of poor bonding copper layer covered in the polishing surface, seriously affecting the polishing child. In order to improve the service life of the fixture, the exposed part of the fixture must be covered with polyvinyl chloride tape, or coated with polyvinyl paste resin or green hook glue, and then baked and melted into a film on the 200° oven, so that the film can reach a certain thickness. Then use a knife to scrape off the insulating film at the contact point, exposing the metal surface to facilitate conduction. Activate the contact point in the lye each time you use it.
(4) The electrical conductivity of the fixture. The current density used in electrochemical polishing is relatively high. Under normal circumstances, a groove of current through up to thousands of amperes, fixture design and production to consider the parts of the maximum current to be able to pass through the conductive plate of the fixture without excessive hot, aluminum plate per square millimeter through the current does not exceed 4A is appropriate, fixture temperature rise is too high, not easy to lift, easier to make the fixture lose elasticity and clamping parts ability, The contact area of the fixture connecting parts should be reasonable. According to the shape of the polished surface and the distribution of the current in the solution, the conductive contact point should be appropriately increased, at least no small D-3 points, the contact point between the conductive plate and the part must be tight and firm, and it must not be loosened during the polishing process. For the reset of the larger part, the screw can be tightened, and the smaller installation mark is allowed. Aluminum fixtures need to be corroded with hot alkali before use to remove the oxide film generated after aluminum is placed in the air for a long time, affecting the normal introduction of current.
(5) Polishing tank level height. In electrochemical polishing processes, especially polishing solutions containing glycerin or additives. A large amount of foam will float on the liquid surface. In order to prevent foam from overflowing outside the tank and facilitate the adjustment of the relative density of the sowing liquid, the liquid surface should be left with space. Therefore, the liquid level of the polishing tank should be 300mm lower than the total height of the tank. When designing the height of the groove, the height of the groove /i=250 + 50 + a+300 (mm) = a+ 600(mm) can be obtained according to the maximum polishing part length U), 250mm from the bottom of the groove, 50mm from the liquid level plane, and 300mm from the liquid level plane to the notch.
(6) Polishing groove anode moving device. The anode rod for placing the fixture and parts is movable, and the moving rate is reciprocating 10 to 20 times per minute, and the left and right stroke is 100mm.